Lithium-Ion Batteries
To conquer the global energy transition towards renewable energy sources reliable energy storage is required. Lithium-ion batteries (LIBs) are dominating the market, especially for electric vehicles and portable devices. Intensive research is performed by industry and government to build an energy-sustainable economy.
The cathode is the critical part of LIBs determining the cell performance and overall cost. Features of LIBs include among others a high power density, comparable long lifetime, and high charge/discharge rates.
Challenges
Commonly, cathodes are composed of expensive elements such as Co and tend to react with the electrolyte. Plenty of cathode materials emerged to bring down the cost by switching to more earth-abundant elements, such as Mn or Fe. More severe is the degradation of cathode material due to the reaction with the electrolyte. Additives to the electrolyte may enhance the lifespan but functional coatings of the cathode material show a more promising path1. However, plenty of functional coatings are available and all of these behave differently on different cathode materials demanding a vast amount of research. Here, we want to give a brief insight into oxide-based coatings applied by atomic layer deposition (ALD)2.
Coating cathode-powder materials is a challenging task. ALD is the superior technique for this application due to the possibility of conformal coatings with enormous aspect ratios. Small modifications have to be made to the conventional ALD setup as the powder needs to be in motion during the coating process to prevent agglomeration. Steven M. George and his group are the pioneers of powder ALD in the beginning of the 21st century2. They developed powder coatings in fluidized beds or rotary vessels to obtain agglomeration-free thin conformal coatings.
Oxide-Based Coating
Oxide-based coatings enhance chemical stability and provide pathways for Li-ion diffusion while fully covering the cathode powder surface. Many oxides have been investigated such as ZnO, Al2O3, SnO2, ZrO2, and TiO2. Here we just want to talk briefly about ZnO and Al2O3.
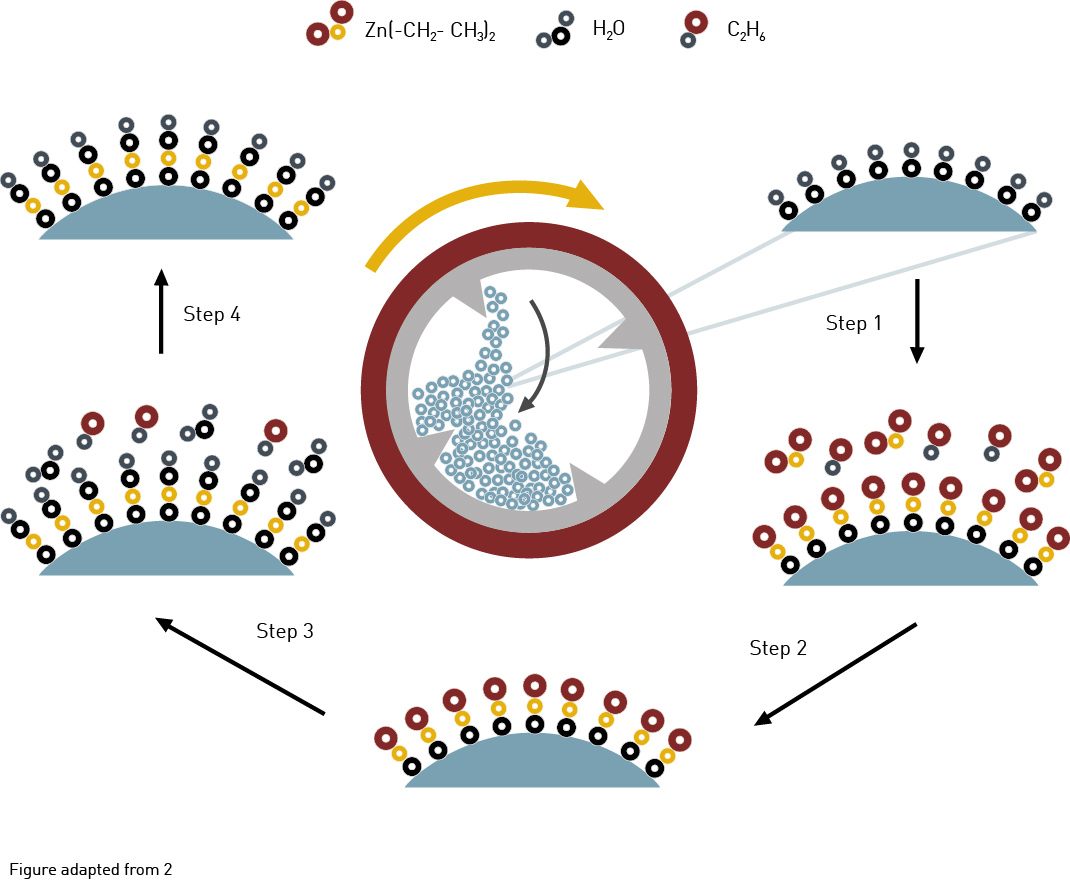
The ALD process is similar to conventional CVD processes but the reaction of the precursors is limited to surface reactions. Precursors are pulsed into the reactor in a cycled manner separated by a purge cycle in between. Figure 1 shows the four-step ALD process of ZnO using Diethylzinc (DEZn) and Water (H2O) as precursors. First, DEZn reacts with the OH-passivated surface to O-Zn-C2H5 and gaseous C2H6. Further exposure must not lead to a reaction with the surface to facilitate the self-limiting nature of the ALD process. Residual gases are removed in the purging step. Next, the surface is exposed to the co-reactant H2O which removes the organic ligand and forms again an OH-passivated surface. In the last step, the reactor is purged and the reaction cycle starts again. Due to the self-limitation of the first and second steps, conformal coatings with precise thickness control can be fabricated. Only a small temperature window is available for self-limiting growth that depends on the substrate and the chosen precursors.
Al2O3 is the most investigated coating due to its low cost and the well-developed ALD process. Thick coatings lead to a reduced initial capacity of the battery cell demanding thin coatings. Standard precursors for this process are Trimethylaluminum (TMAl) and H2O. Thin coatings of LiMn2O4 by ZnO showed enhanced cycle stability and capacity compared to Al2O3 and ZrO2.
A comprehensive review of cathode powder coating processes including oxides, phosphates, fluorides, and more is given in 2.
References:
- Kaur, G. & Gates, B. D. Review—Surface Coatings for Cathodes in Lithium Ion Batteries: From Crystal Structures to Electrochemical Performance. J Electrochem Soc 169, 043504 (2022) doi: 10.1149/1945-7111/ac60f3.
- Lee, M. et al. Powder Coatings via Atomic Layer Deposition for Batteries: A Review. Chemistry of Materials 34, 3539–3587 (2022) doi: 10.1021/acs.chemmater.1c02944.